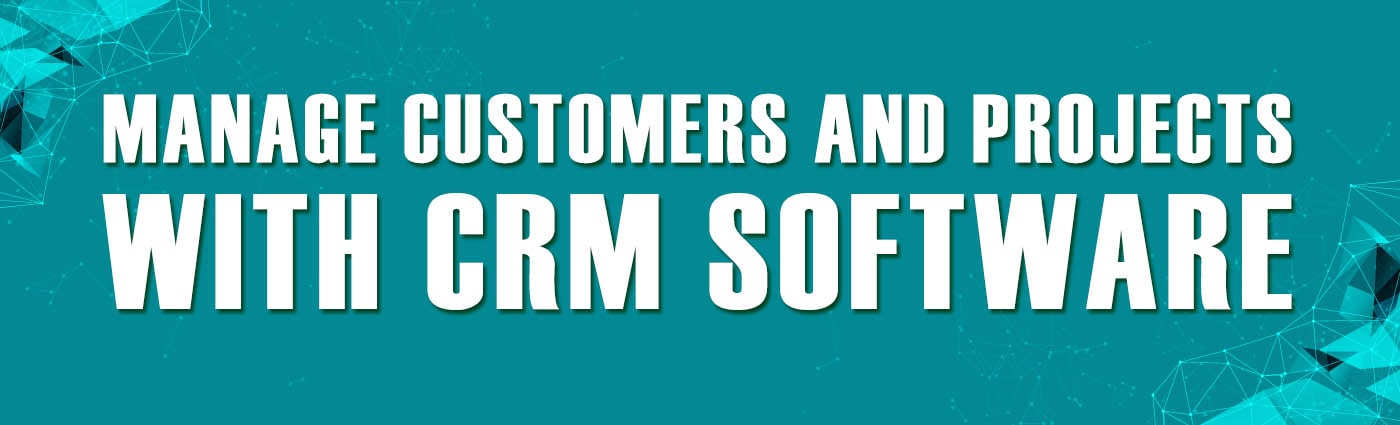
As the Inside Sales Manager for Alchemy-Spetec, I am responsible for keeping our lead, customer, and project data in order. Our busy sales and marketing team needs to access this information quickly and accurately. Precise, contextual, and quick accessibility of these systems gives our team a powerful, painless, and rapid advantage over our competitors that are stuck using outdated technology and processes.
We can organize all of our leads, customers, and potential projects by using some type of Customer Relationship Management software. In fact, we are currently using two separate CRM software programs for our sales department. Our main customer database is stored in Salesforce. The entire team has access to this platform and can log in regularly for up-to-date customer information, sales numbers, etc.
In order to keep our Salesforce database lean and relevant, our inside sales efforts are conducted within the fast and efficient Salesmate CRM to track opportunities as they develop. Salesforce can be extremely powerful for larger organizations who require limitless customization and reporting, while Salesmate is an excellent intuitive and lightweight CRM for organizations with a smaller budget. Contractors looking for a CRM may also want to consider the Alchemy-Spetec custom version of Estimate Rocket. Estimate Rocket is a multi-purpose tool for creating job estimates, calculating material needs, generating financial reports, tracking customers/projects, and more! The Alchemy-Spetec customized version of Estimate Rocket features our geotech material estimation calculators built in. Read more here.
These are just a few of the many CRMs on the market. We strongly encourage you to do your own research and choose the CRM that best suits your business needs. If you have any further questions on the subject, feel free to call Alchemy-Spetec at 404-618-0438 and ask for the Inside Sales Manager, David Park. We offer a unique understanding of proven and innovative CRM solutions that can optimize your sales efforts moving forward.
Want information on Alchemy-Spetec products?

