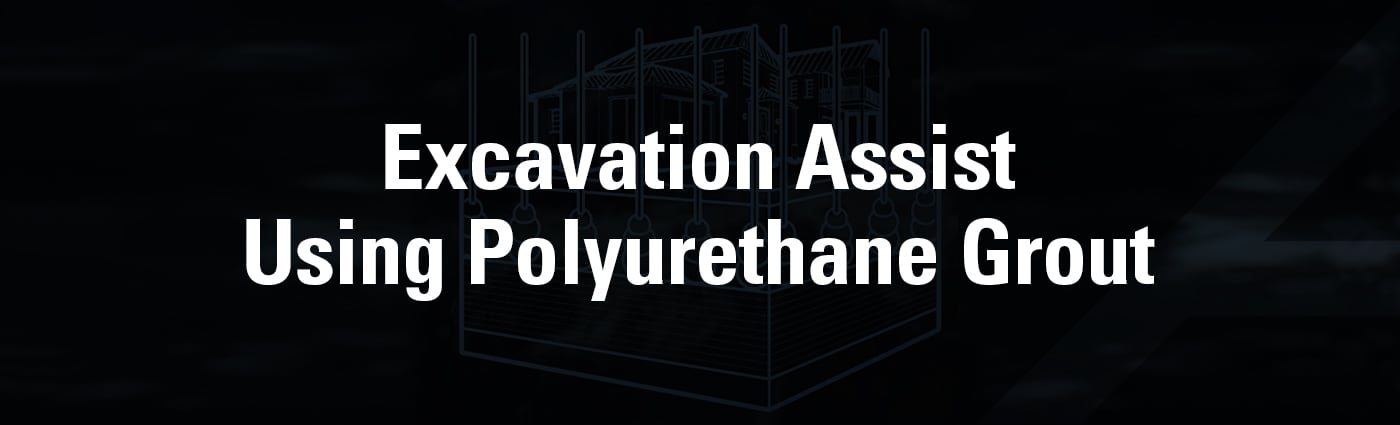
This post is part of the Alchatek Contractor Lens series, featuring views, news & case studies written by our customers. This article was written by Jay Silver and originally posted on the Helicon blog.
When Excavation Gets Tight, Think Beyond Sheet Piles
Excavating near an existing structure — like a home, commercial building, or utility line — often requires soil support to avoid collapse or damage. For decades, the go-to solution has been sheet piling: driving steel sheets into the ground to create a temporary shoring wall.
But sheet piles come with serious downsides:
- High cost
- Vibration risks to nearby structures
- Heavy equipment needs
- Limited accessibility in tight areas
Today, there’s a smarter, faster, and more cost-effective alternative for excavation support: polyurethane injection permeation grouting.
What Is Polyurethane Grout Injection for Excavation Assist?
Helicon uses a permeation grout called AP Soil 600, a low-viscosity polyurethane resin, to stabilize soil and build a temporary underground wall. This non-expanding material seeps into fine-grained soils (like sand), then hardens into a concrete-like mass — turning unstable ground into a solid excavation shoring wall.
This “grout curtain” supports the soil adjacent to your dig site, providing excavation assist without the need for steel sheets or heavy machinery.
Common Use Cases for Polyurethane Shoring Walls
Excavations next to homes or commercial buildings
Tight-access job sites where pile driving equipment won’t fit
Urban infill projects with vibration-sensitive neighbors
Value-engineered alternatives to high-cost sheet pile installation
Projects with depth requirements up to ~15 feet
Sheet Piles vs. Polyurethane Injection
Feature |
Sheet Piles |
Polyurethane Injection (AP Soil 600) |
Cost |
High (steel + installation) |
Significantly lower |
Vibration |
High — risk to nearby buildings |
Very low — minimal disruption |
Access Requirements |
Requires large equipment |
Works in tight or restricted areas |
Noise |
Loud during driving |
Quiet installation |
Environmental Impact |
Steel removal adds cost |
Grout is inert and stays in place |
Max Effective Depth |
30–60+ ft |
Up to 15 ft (ideal range) |
How It Works: The Grout Curtain Process
1. Plan and Mark
The contractor provides excavation depth and layout. Helicon’s team maps out injection lines using stakes or string to ensure precision.
2. Drill Injection Holes
Using compact equipment, injection rods are installed at a slight 3–5° angle away from the excavation. Rods are spaced 18″ apart, and for depths >8 feet, a second staggered row is added 18″ behind the first.
3. Inject AP Soil 600 Grout
Each rod is used to inject grout in 1-foot intervals from bottom to top:
- Start 2 feet below planned excavation depth
- Inject 1 gallon per vertical foot
- Grout permeates and hardens in ~2 minutes per foot
- Stops 1 foot below surface to avoid breakout
The non-expanding grout permeates the soil, turning it into a rigid, cohesive wall capable of holding back earth during excavation.
4. Excavate Safely
Once cured (typically within 24 hours), excavation can begin — but mechanical equipment must stay 2+ feet away from the grout wall. Final trim is done by hand or hydro-vac.
Soil Types That Work Best
AP Soil 600 is designed for permeation, not expansion. It’s ideal for:
✅ Sand
✅ Fine silts
✅ Granular soil types
⚠️ Less effective in:
- High plasticity clay (which resists permeation and may not need shoring)
- Organic material or very dense clay (which can fracture or lens)
That’s why soil boring reports or geotechnical testing are important for project design.
Depth Recommendations
Excavation Depth |
Injection Strategy |
≤ 8 ft |
Single row (18” spacing) |
8–15 ft |
Double staggered row |
> 15 ft |
Sheet piles may be better |
Helicon’s polyurethane grout walls are most effective up to 15 feet. Beyond that, multiple injection rows become inefficient, and other structural shoring may be needed.
Cost Savings & ROI
Switching from sheet piles to Helicon’s polyurethane grout method can save:
- Tens of thousands on residential jobs
- Up to six figures on larger commercial projects
Savings come from:
- No need for steel or removal
- Smaller crews and equipment
- Shorter install times
- No costly vibration damage
Combine with Underpinning When Needed
When adjacent structures need more than soil support, Helicon can pair permeation grouting with:
- Push piers (steel-driven deep supports)
- Drilled piers (poured concrete or steel)
This hybrid approach is ideal for:
- Older buildings
- Structures with active settlement
- High-load foundations near deep excavation
Real-World Examples
On a commercial project, the contractor and engineer originally planned to use traditional sheet piles for shoring to support the foundation of a commercial building. Helicon collaborated with the engineer to develop a value-engineered alternative: a polyurethane grout curtain combined with steel push piers installed under the building’s foundation. The shoring wall and underpins were completed within five days, excavation proceeded safely, and the client saved over $300,000 compared to the original sheet pile proposal.
On a recent project with access constraints, Helicon installed a polyurethane grout curtain within 2 feet of a residential foundation. Traditional sheet piles weren’t an option due to equipment access and budget. The wall was in place within two days, excavation followed safely, and the client saved over $70,000 compared to a sheet pile proposal.
Safety Guidelines
- Injection starts 2’ below excavation depth
- Do not excavate within 24” of cured grout with equipment
- Always hand dig near the grout wall
- Excavation limit line should be marked 33” back from rods (accounting for rod angle)
Why Engineers and Contractors Choose Helicon
- Florida-based foundation experts
- Proven track record in geotechnical solutions
- Fast mobilization and project turnaround
- Seamless integration with GCs, engineers, and owners
- Full service: injection + underpinning + stabilization
Optimize Your Excavation Support Plan
If you’re a contractor, builder, or geotechnical engineer working on an excavation project in tight quarters, don’t default to sheet piles. Helicon’s polyurethane injection method is often:
- Faster
- Cheaper
- Cleaner
- More flexible
Helicon specializes in value-engineering shoring solutions that reduce project costs and risks while maintaining structural safety and soil integrity.
Let’s Put Your Excavation Project on Solid Ground
Have a project where you’re excavating near a structure? Let’s collaborate. Helicon offers:
Want more information on Alchatek's geotech solutions?
