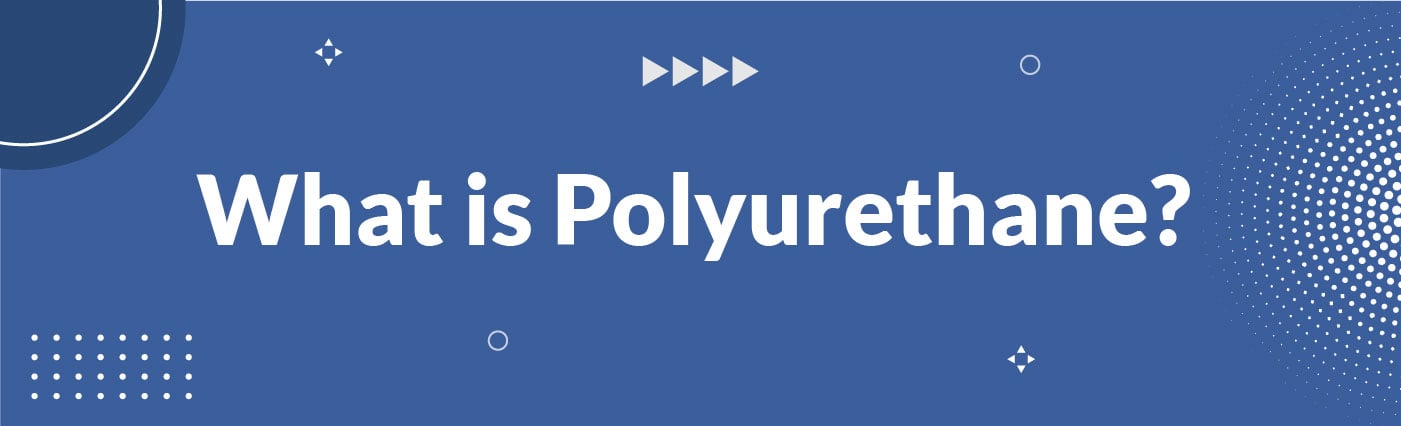
This post is part of the Alchemy-Spetec Contractor Lens series, featuring views, news & case studies written by our customers. This article, written by Brian Dalinghaus of Dalinghaus Construction, provides an overview of polyurethane concrete repair material. If you're an Alchemy-Spetec customer and you'd like to discuss writing content for our blog, please send an email to marketing@alchemy-spetec.com today!
Perhaps a foundation repair contractor has suggested polyurethane foam for deep injection, void fill, or slab lifting/leveling, but you’re not so sure about pumping “plastic” into the earth or underneath your home. You’re probably wondering: is polyurethane environmentally friendly? Is it effective?
If you’re concerned about the use of polyurethane for foundation repair and soil densification or just want to know more general information about PU, this article is for you.
Dalinghaus Construction Inc. has been in the foundation repair game since 2015. We have over 100 years of combined foundation repair experience and have serviced thousands of foundations in Southern California and Arizona via polyurethane-related repairs. We know everything there is to know about polyurethane and we’re here to share.
In this article, you will learn the definition of polyurethane, its history, many general uses, and how polyurethane foam is utilized in foundation repair.
What is Polyurethane?
Before you pump gallons of polyurethane foam underneath your home or into the soil around your property, you probably want to know what exactly it is.
Polyurethane Definition
Polyurethane is a synthetic resin compound comprised of carbamate/urethane groups linked to polymer units, often abbreviated as PU or PUR. In other words, polyurethane is a combination of chemicals/compounds that react to create a plastic-like substance. As a solid, polyurethane has an open-cellular structure – which is a foam.
Polyurethane foam, utilized for many purposes including insulation, sound-proofing, and foundation repair, is created by the chemical reaction of Diisocyanates and polyols (both of which are derived from organic crude oil). Because polyurethane is comprised of organic material, it is environmentally friendly and does not contribute to an increased eco-footprint.
According to the Polyurethane definition, it is not a plastic. Technically, the elongated flexible polymer molecules that make up thermoset polyurethanes categorize this material as an elastomer (a natural or synthetic polymer having elastic properties, e.g., rubber).
Polyurethane foam is a safe, eco-friendly option to densify weak, non-load-bearing soil, void fill beneath your foundation following a lift/stabilization and relevel slabs.
History of Polyurethane
Polyurethane was invented in 1937 by the renowned German Professor Dr. Otto Bayer. Dr. Otto Bayer was an industrial chemist and worked for IG Farben – spearheading the research team that discovered polyaddition (the key to synthesis for polyurethanes by combining polyol and polyisocyanate).
Polyurethane first enjoyed widespread use in World War II as a rubber substitute. Polyurethane was utilized as airplane finishes, various coatings, and to create flame-retardant clothing. By the 1950s, Polyurethane was utilized for many different applications: couch cushion foam, rigid foams, elastomers, and adhesives.
Today, polyurethane is utilized for a wide variety of applications: mattresses, shoe soles, car seats, insulation, and even pacemakers. Polyurethane is a “behind the scenes” product, often hidden behind a layer of fabric, plastic, or other encasing material.
Due to its prevalence, in everything from car seats to pacemakers, it’s truly difficult to grasp the full scope and impact of polyurethane in everyday life – however, its importance in the foundation repair game is easy to explain.
Polyurethane and Foundation Repair
The foundation repair industry uses polyurethane foam primarily for soil densification, void fill, and lifting/leveling slabs back into place. Polyurethane foam is an injectable polyol and isocyanate resin sealant, insulation, grout which expands upon application providing void fill, structural support, and re-leveling properties.
The polyurethane foam is installed via an application gun: the polyols (a type of alcohol, containing multiple hydroxyl groups) and diisocyanate/polymeric isocyanate are pumped separately, but simultaneously. The chemicals combine and react after exiting the application gun.
The foam then expands, filling the void, densifying the soil, or lifting the slab back into place. In short, polyurethane has incredible expansive properties, allowing it to fill voids evenly and with ease – providing strength and support to the affected structure.
Here at Dalinghaus Construction Inc., we use Alchemy-Spetec's AP Lift 430 (which has been certified by Truesdail Labs to NSF/ANSI 61-5 – meaning it’s approved for contact with drinking water).
AP Lift 430 is:
- Waterproof (Hydrophobic)
- Noninvasive (Install Process is More Efficient and Replacing Concrete)
- Nonpolluting (NSF Approved for Contact with Potable Water)
In addition, AP Lift 430 weighs approximately 3 pounds per cubic foot and reaches 90% compression strength in only 15 minutes. And, finally, polyurethane can hold 7,200 pounds per square foot. In short, polyurethane is a fantastic solution for foundation repair and hillside stabilization needs.
Polyurethane Foam is Safe, Effective, and Environmentally Friendly
In this article, you learned the definition of polyurethane, how it was invited by Dr. Otto Bayer, the wide spectrum of uses, and how polyurethane foam is utilized in foundation repair and construction. You also learned that polyurethane is a safe and effective product. Dalinghaus Construction has helped hundreds of homeowners and offers an array of services, including carbon fiber crack repair, steel pier underpinning, and more.
Click here if you live in Southern California or Arizona and would like to book a free foundation inspection.
Want more information on polyurethane repair products?

