-2.png?width=1400&name=Reminder%20-%202019%20Fall%20Training%20on%20October%209th%20%26%2010th%20(1)-2.png)
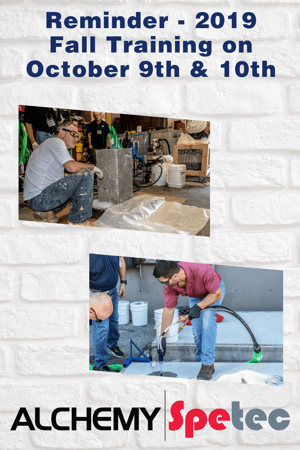
You still have a chance to sign up for Fall 2019 Training while there are still spots left. Don't miss this critical opportunity to turbo-charge your business!
October 9th & 10th, 2019 at Alchemy-Spetec HQ in Tucker, GA
Get ready for a thorough education in Leak Seal, Slab Lifting, Soil Stabilization and the Alchemy-Spetec Deep Lift™ process. You’ll get hands-on training from a technical staff with decades of on-the-job experience.
Wednesday - Leak Seal
- Leak Seal Product Line Overview
- Curtain Grouting
- Permeation Grouting
- Leak-Seal Product Mixing
- Pump & Packer Overviews
- Leak-Seal Accessories
- Municipal Applications
- Live Injection Demos
- Open Discussions
Thursday - Geotech
- Geotech Product Line Overview
- Soil Stabilization
- Geotech Product Mixing
- Rig & Mobile System Overviews
- Geotechnical Accessories
- Slab Lifting Live Demo
- Deep Lift™ Overview
- Soil Testing with the
- GPR & Penetrometer
- Maintenance Discussions
- Pricing / Estimating / Cost Savings
- Open Discussions

Participants receive a Samsung tablet loaded with training material.
Your Instructors:
Stephen C. Barton (President/CEO), Jim Spiegel (VP Sales & Business Development), Andy Powell (Southeastern Regional Manager), Anthony Sandone (Eastern Regional Manager), Charlie Lerman (Western Regional Manager), and Michael Binyaminov (Western Sales Representative).
Topics:
Repair Seawalls,
Equipment & Accessories,
All Posts,
Lift Slabs,
NSF Certification,
Seal Leaks,
Stabilize Soil,
Business Tips,
Repair Cracks,
Waterstop,
Deep Lift,
Floor Repair,
Fill Voids,
Engineer Resources
-1.png?width=1400&name=Reminder%20-%202019%20Fall%20Training%20on%20October%209th%20%26%2010th%20(1)-1.png)
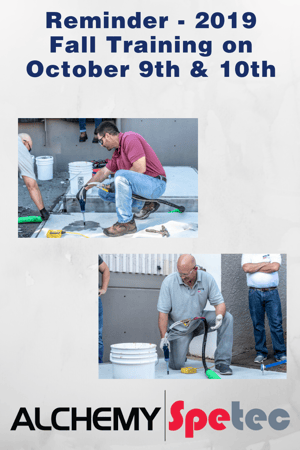
Sign up for Fall 2019 Training while there are still spots left!
October 9th & 10th, 2019 at Alchemy-Spetec HQ in Tucker, GA
Get ready for a thorough education in Leak Seal, Slab Lifting, Soil Stabilization and the Alchemy-Spetec Deep Lift™ process. You’ll get hands-on training from a technical staff with decades of on-the-job experience.
Wednesday - Leak Seal
- Leak Seal Product Line Overview
- Curtain Grouting
- Permeation Grouting
- Leak-Seal Product Mixing
- Pump & Packer Overviews
- Leak-Seal Accessories
- Municipal Applications
- Live Injection Demos
- Open Discussions
Thursday - Geotech
- Geotech Product Line Overview
- Soil Stabilization
- Geotech Product Mixing
- Rig & Mobile System Overviews
- Geotechnical Accessories
- Slab Lifting Live Demo
- Deep Lift™ Overview
- Soil Testing with the
- GPR & Penetrometer
- Maintenance Discussions
- Pricing / Estimating / Cost Savings
- Open Discussions

Participants receive a Samsung tablet loaded with training material.
Your Instructors:
Stephen C. Barton (President/CEO), Jim Spiegel (VP Sales & Business Development), Andy Powell (Southeastern Regional Manager), Anthony Sandone (Eastern Regional Manager), Charlie Lerman (Western Regional Manager), and Michael Binyaminov (Western Sales Representative).
Topics:
Repair Seawalls,
Equipment & Accessories,
All Posts,
Lift Slabs,
NSF Certification,
Seal Leaks,
Stabilize Soil,
Business Tips,
Repair Cracks,
Waterstop,
Deep Lift,
Floor Repair,
Fill Voids,
Engineer Resources
.png?width=1400&name=Specifications%20for%20Permeation%20Grouting%20with%20Polyurethane%20(2).png)
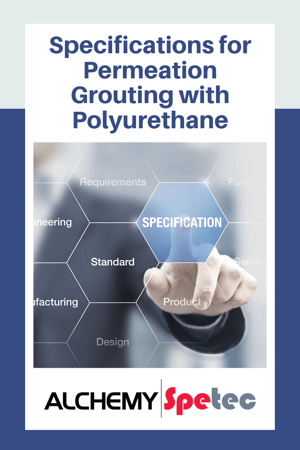
Today, we’ll take a look at the specification Permeation Grouting with Polyurethane. The specification includes documentation on the following:
- Stabilization, consolidation, and binding of water bearing soils through permeation injection of polyurethane resin creating a solid mass of soil and rigid resin.
- Creation of a barrier in water bearing soils to reduce water migration through permeation injection of polyurethane resin creating a solid mass of soil and rigid resin.
Click this link, Permeation Grouting with Polyurethane, to view a PDF of the specification. It thoroughly documents the installation process for one component, moisture activated, low viscosity, hydrophobic polyurethane (in our case, AP Soil 600 stabilization foam). For a copy of the specification in Microsoft Word format, please call Alchemy-Spetec at 404-618-0438.
If you scroll to the bottom of the Alchemy-Spetec downloads page, you’ll see a list of engineering specifications for Concrete Repair with Polyurethane.
Want more information on Alchemy-Spetec products?


Topics:
All Posts,
Stabilize Soil,
Engineer Resources
.png?width=1400&name=Reminder%20-%202019%20Fall%20Training%20on%20October%209th%20%26%2010th%20(2).png)
Don't forget to sign up for Fall 2019 Training!

October 9th & 10th, 2019 at Alchemy-Spetec HQ in Tucker, GA
Get ready for a thorough education in Leak Seal, Slab Lifting, Soil Stabilization and the Alchemy-Spetec Deep Lift™ process. You’ll get hands-on training from a technical staff with decades of on-the-job experience.
Wednesday - Leak Seal
- Leak Seal Product Line Overview
- Curtain Grouting
- Permeation Grouting
- Leak-Seal Product Mixing
- Pump & Packer Overviews
- Leak-Seal Accessories
- Municipal Applications
- Live Injection Demos
- Open Discussions
Thursday - Geotech
- Geotech Product Line Overview
- Soil Stabilization
- Geotech Product Mixing
- Rig & Mobile System Overviews
- Geotechnical Accessories
- Slab Lifting Live Demo
- Deep Lift™ Overview
- Soil Testing with the
- GPR & Penetrometer
- Maintenance Discussions
- Pricing / Estimating / Cost Savings
- Open Discussions
Participants receive a Samsung tablet loaded with training material.
Your Instructors:
Stephen C. Barton (President/CEO), Jim Spiegel (VP Sales & Business Development), Andy Powell (Southeastern Regional Manager), Anthony Sandone (Eastern Regional Manager), Charlie Lerman (Western Regional Manager), and Michael Binyaminov (Western Sales Representative).
Topics:
Repair Seawalls,
Equipment & Accessories,
All Posts,
Lift Slabs,
NSF Certification,
Seal Leaks,
Stabilize Soil,
Business Tips,
Repair Cracks,
Waterstop,
Deep Lift,
Floor Repair,
Fill Voids,
Engineer Resources
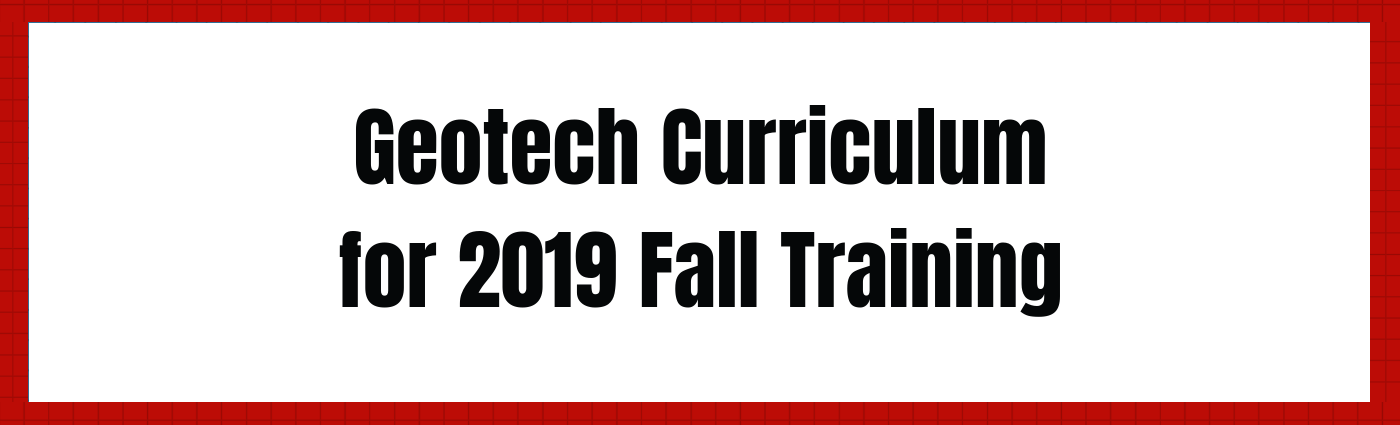
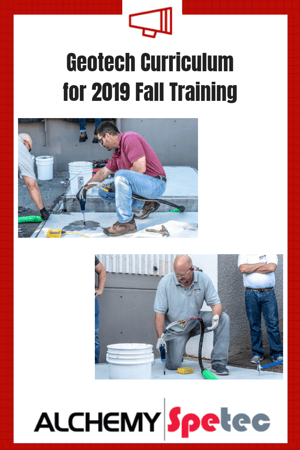
Get ready for a thorough education in polyurethane slab lift/soil stabilization geotech products and applications on Thursday, October 10th (October 9th is leak seal day), 2019 at Alchemy-Spetec HQ in Tucker, GA. You’ll get hands-on training from a technical staff with decades of on-the-job experience. Registration includes both days, but we’ll take a close look at the geotech curriculum in today’s blog post…
The schedule on Thursday, October 10th includes education on the Alchemy-Spetec geotech product line, soil stabilization, slab lifting, the Deep Lift™ process, rig & mobile lifting systems, geotech accessories, soil testing (ground penetrating radar, penetrometer), pricing and estimating. There will also be live geotech demos, product mixing demos, and open discussions for sharing job related tips and solutions from the field.
Your instructors have years of experience providing technical support for contractors across the country. You can look forward to presentations, demos and/or discussions lead by Stephen C. Barton (President/CEO), Jim Spiegel (VP Sales & Business Development), Andy Powell (Southeastern Regional Manager), Anthony Sandone (Eastern Regional Manager), and Charlie Lerman (Western Regional Manager).
Participants will receive a Samsung tablet loaded with leak seal training material.
Sign up while there's still space available...

Topics:
Equipment & Accessories,
All Posts,
Lift Slabs,
Stabilize Soil,
Business Tips,
Deep Lift

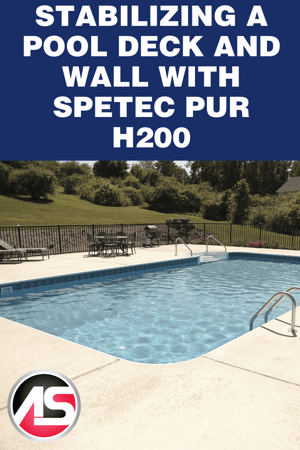
Today’s guest blogger is Bill Stivers, an experienced salesman at Alchemy-Spetec distributor Sunshine Supply.
As a Salesman at Sunshine Supply, I’ve dealt with a lot of leak seal products over the years. But I don’t often get the chance to try them out on my own property. I recently, however, had an issue with a leaking swimming pool in my own back yard. Water was draining through the seams between the slabs of my pool deck and causing erosion. In addition, ground squirrels and rabbits had been digging around the area over the years, causing further issues with soil displacement. The pool deck was destabilized along with the wall surrounding the pool. They had both slipped about a half an inch down a small hill on one side. Some bricks around the pool had settled about 2 inches. My extensive experience in this field told me that this was just the beginning of a much more serious problem. The leaking water had to be contained and the soil around the structures had to be stabilized immediately.
Due to my position at Sunshine Supply, I am familiar with a wide range of leak seal products, and there was one that I knew would be ideal for this job: Spetec PUR H200. We injected deep into the soil on the hillside via 6-foot injection pipes. We used an F-Valve to simultaneously inject water along with the resin to jump-start the reaction process. (The wet soil would have caused the resin to react anyways, but the added water kick started the reaction process for a quicker install of the material.) This process prevents the wall and pool deck from further slippage by stopping the seeping water and stabilizing the supporting soil.
If you live in any of the following areas and want to buy your leak seal supplies from distributors with expert knowledge of the products, make sure you contact Sunshine Supply at any of the following locations:
Want more information on Alchemy-Spetec leak seal products?

Topics:
All Posts,
Seal Leaks,
Stabilize Soil
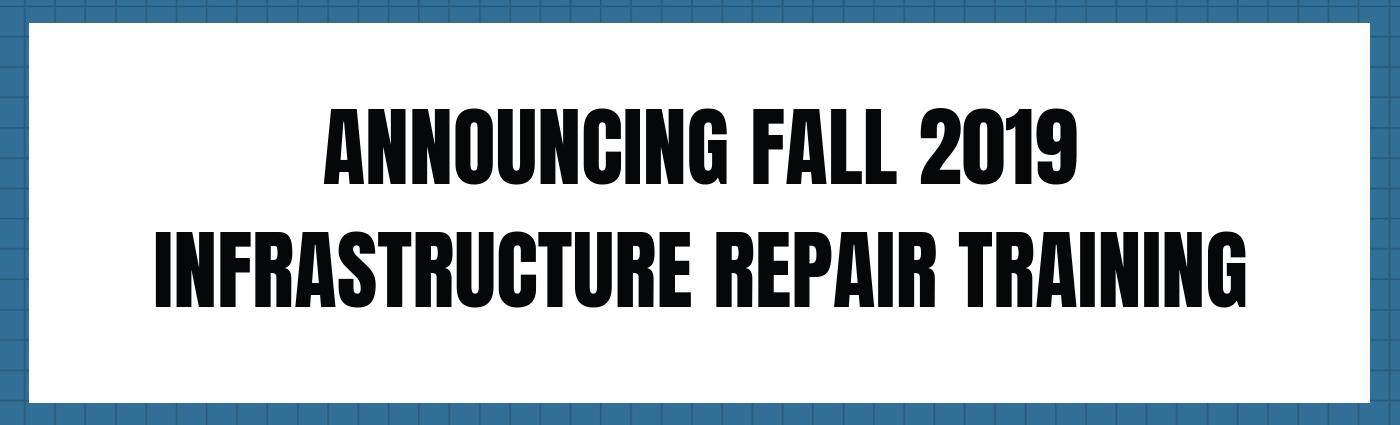
Leak Seal & Geotech Products & Procedures
October 9th & 10th, 2019 at Alchemy-Spetec HQ in Tucker, GA
Get ready for a thorough education in Leak Seal, Slab Lifting, Soil Stabilization and the Alchemy-Spetec Deep Lift™ process. You’ll get hands-on training from a technical staff with decades of on-the-job experience.
Wednesday - Leak Seal
- Leak Seal Product Line Overview
- Curtain Grouting
- Permeation Grouting
- Leak-Seal Product Mixing
- Pump & Packer Overviews
- Leak-Seal Accessories
- Municipal Applications
- Live Injection Demos
- Open Discussions
Thursday - Geotech
- Geotech Product Line Overview
- Soil Stabilization
- Geotech Product Mixing
- Rig & Mobile System Overviews
- Geotechnical Accessories
- Slab Lifting Live Demo
- Deep Lift™ Overview
- Soil Testing with the
- GPR & Penetrometer
- Maintenance Discussions
- Pricing / Estimating / Cost Savings
- Open Discussions

Participants receive a Samsung tablet loaded with training material.
Your Instructors:
Stephen C. Barton (President/CEO), Jim Spiegel (VP Sales & Business Development), Andy Powell (Southeastern Regional Manager), Anthony Sandone (Eastern Regional Manager), Charlie Lerman (Western Regional Manager), and Michael Binyaminov (Western Sales Representative).
Topics:
Repair Seawalls,
Equipment & Accessories,
All Posts,
Lift Slabs,
Seal Leaks,
Stabilize Soil,
Business Tips,
Repair Cracks,
Waterstop,
Deep Lift,
Floor Repair
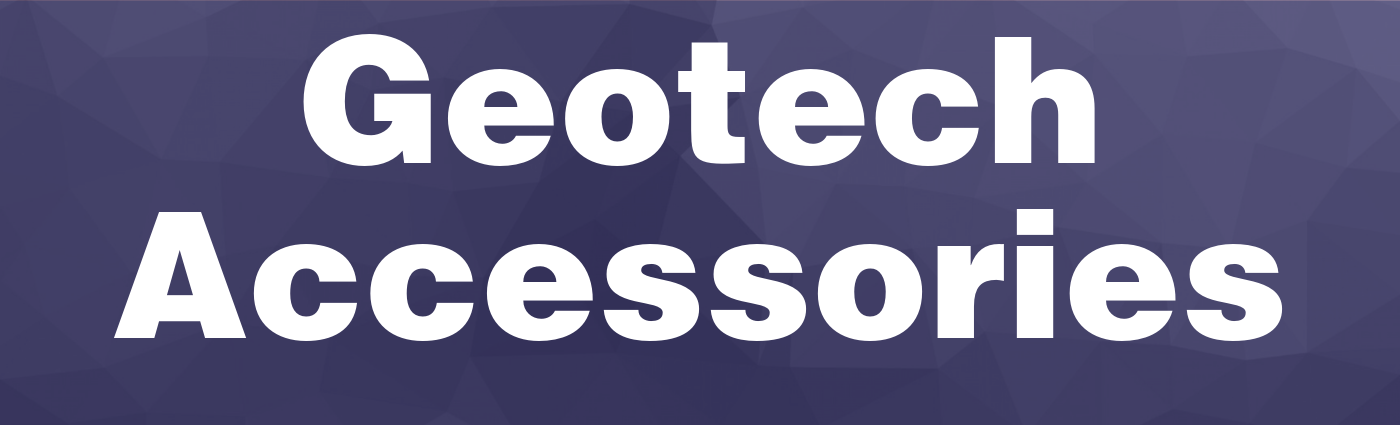
Alchemy-Spetec offers a variety of accessories for use with the geotech product line. In this post, we'll take a brief tour. If you have any questions about these products, don't hesitate to call us at 404-618-0438.
Slab Lifting Gun & Stand Up Attachment
Two-component resin injection gun manufactured specifically for lifting concrete slabs, designed to handle back-pressure. As the essential piece of foam jacking equipment for Alchemy-Spetec’s expanding polyurethane foams, the resin injection gun provides highly-efficient concrete leveling. The attachment allows the user to stand while operating the gun.

PolyBadger Lifting System
The Alchemy-Spetec PolyBadger lifting system is tough and compact. This system is an affordable entry-level option for new contractors, as well as an extremely portable addition to the experienced contractor’s arsenal. The PolyBadger is a lot less expensive than your standard 20 foot trailer rig. The set up is simple and requires minimal equipment. The entire system can easily fit in the back of a pickup truck!. The genius of the PolyBadger is the auto calibrator. It keeps the flow of A and B on ratio, eliminating the possibility of a crossover in the gun or the whip hose.

As the essential piece of concrete leveling equipment, the PMC plural component hydraulic proportioner is used to inject AP two-component structural polyurethane foams for Slab Lifting, Filling Voids and Soil Stabilization. Rugged and dependable, this line of concrete leveling equipment utilizes relays and circuit breakers instead of circuit boards, vastly increasing reliability and preventing maintenance problems. Read more here...
AP Flush 121
Reusable, biodegradable, high performance pump flush that is friendly to the environment and does an excellent job flushing out pumps.
AP Flush 125
Water based gun flush specifically used for flushing out the MixMaster impingement gun. Also used to protect concrete from resin stains.
AP Soak 130
AP Soak 130 is a reusable, non-flammable solvent for cleaning cured resin from metal components.
AP Lube 190
AP Lube 190 is a lubricant for preventing isocyanate from setting up inside pumps or hoses.
Spetec Gel Reinforcing Agent
Spetec Gel Reinforcing Agent is an acrylic latex additive used to increase the strength and flexibility of our AG series of acrylic gels.
Want more information on Alchemy-Spetec geotech products?

Topics:
All Posts,
Lift Slabs,
Stabilize Soil,
Deep Lift
.png?width=1400&name=Banner%20AP%20Lube%20190%20(1).png)
Spetec Gel Reinforcing Agent is an acrylic latex additive used to increase the strength and flexibility of our AG series of acrylic gels: Spetec AG100, Spetec AG200 and AP SoilGel 200.
Advantages
- Improved adhesion.
- Increased hydrostatic pressure resistance.
- Improved resistance to wet/dry cycles.
- Improved low temperature flexibility.
- Minimizes hydrophilic shrinkage in dry cycling.
- Solvent free.
- Non-toxic.
Field of Application
- Soil stabilization in below grade structures when used in conjunction with the AG series of products.
- Leak seal in below grade structures when used in conjunction with the AG series of products.
Want more info on Alchemy-Spetec products?


Topics:
Equipment & Accessories,
All Posts,
Seal Leaks,
Stabilize Soil
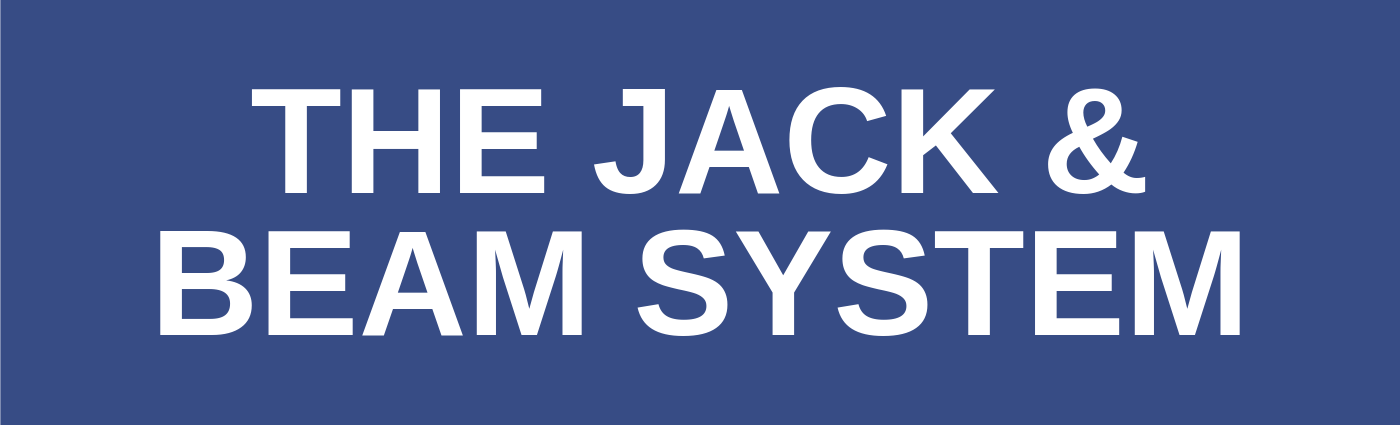
Note: This product is no longer available.
Please see: Jack Attack System.
The Jack & Beam System provides mechanical leverage for guiding the lift direction of slabs or holding them in place while filling voids beneath.
Advantages
Improves accuracy of final slab position.
Helps prevent over-lifting.
Works with a variety of concrete anchors.
Cuts down on wasted foam.
System Components
Two steel structural beams.
Four mechanical jacks.
Accessories kit with chains, hooks and clevices.
Want more information on Alchemy-Spetec Geotech products?

Topics:
All Posts,
Lift Slabs,
Stabilize Soil,
Deep Lift