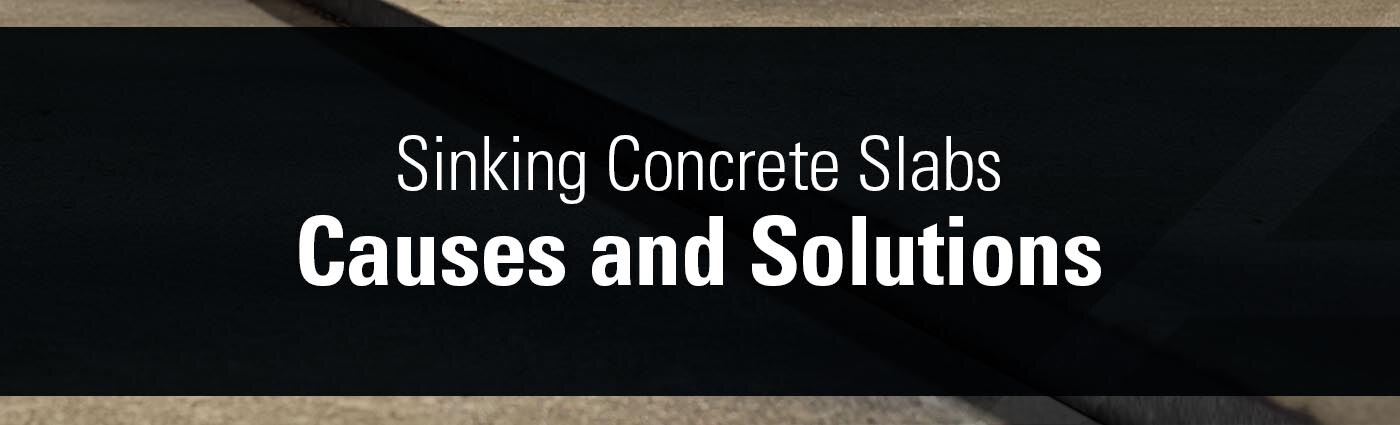
Many property owners face the frustrating issue of sinking concrete slabs. This problem not only affects the appearance of the property but also poses safety risks. Fortunately, modern solutions can effectively address sinking concrete without the need for complete replacement. Let's explore the causes of this common problem and discuss innovative repair methods.
Why Does Concrete Sink?
Several factors contribute to concrete settlement. First, erosion can wash away soil beneath the slab. Second, poor soil compaction during initial construction may lead to instability. Finally, biological decay of buried organic matter can create voids. As a result, the ground beneath the concrete becomes unstable, causing the slab to sink.
The Dangers of Ignoring Sinking Concrete
Failing to address sinking concrete can lead to serious consequences. For instance, uneven surfaces may cause trip hazards, potentially resulting in injuries and liability issues. Moreover, sunken slabs can damage vehicles and expensive structures. In extreme cases, a neglected settlement might even lead to sinkhole formation.
Traditional vs. Modern Repair Methods
Replacing the Slab
Historically, replacing the entire slab was a common solution. However, this approach is messy, time-consuming, and expensive. Additionally, it often involves significant disruption to the surrounding area.
Mudjacking
Another traditional method is mudjacking, which involves pumping a cement-based slurry under the slab. While effective in the short term, the injected material may crack or erode over time, leading to future issues. Furthermore, this technique requires large drill holes and disruptive heavy equipment.
Polyurethane Foam for Lifting Sinking Concrete
In recent years, polyurethane foam lifting has emerged as the preferred method for repairing sinking concrete. This innovative technique offers numerous advantages over traditional approaches.
Strength and Durability
Polyurethane foam features impressive strength, often surpassing that of bedrock. Once injected, the foam continues to gain strength, providing long-lasting support for the repaired slab. As a result, this solution offers exceptional durability compared to other methods.
Minimally Invasive Process
Unlike mudjacking or replacement, foam lifting requires only small drill holes. Consequently, this method causes minimal damage to the existing slab and surrounding area. The lightweight equipment used also reduces the risk of disruption and further soil compaction.
Rapid Results
One of the most significant advantages of polyurethane foam lifting is its speed. The foam cures to 90% strength in just 15 minutes. Therefore, repaired areas can often be used the same day, minimizing disruption to daily activities.
Environmentally Friendly
Alchatek offers polyurethane lifting foams that are NSF-certified to meet strict environmental standards. These products won't leach harmful chemicals into the soil or groundwater. As a result, property owners can feel confident in choosing contractors who offer this eco-friendly solution.
The Foam Lifting Process
The concrete lifting process using polyurethane foam is straightforward and efficient. First, technicians drill small holes in the slab. Next, they inject the foam through these holes. As the foam expands, it fills voids and gently lifts the slab. Finally, the holes are patched, and any cracks are sealed.
Choosing a Professional for Sinking Concrete Repair
When dealing with sinking concrete, it's crucial to hire experienced professionals. Skilled technicians can assess the situation accurately and determine the best course of action. Moreover, they have access to high-quality materials and specialized equipment necessary for effective repairs.
Restoring Your Property's Safety and Value
Addressing sinking concrete promptly can prevent further damage and costly repairs. Property owners can quickly and efficiently restore their concrete surfaces by choosing modern foam lifting techniques. This not only enhances safety but also improves the overall value and appearance of the property.
Fill out this form or call 404-618-0438 for a contractor referral today!
Want more information on lifting sinking concrete with polyurethane?
