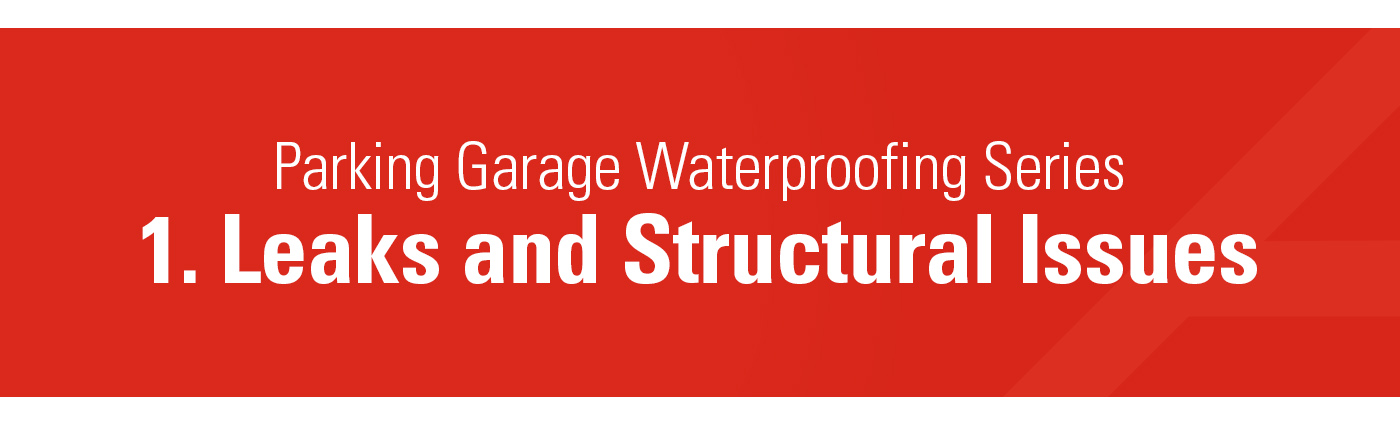
Below-grade parking garages serve as essential components of urban infrastructure. They offer convenient parking solutions, especially in densely populated areas where surface parking is limited. However, these subterranean structures are particularly susceptible to water leaks, which can severely compromise their structural integrity. A compromised structure not only poses safety risks but also leads to costly repairs and decreased property value.
The Detrimental Effects of Water on Concrete
Water leaks in below-grade parking garages are more than just a nuisance; they can be a ticking time bomb for the structure's integrity. Concrete, the primary material used in these garages, is porous by nature. When water seeps into the concrete, it can lead to a variety of problems. One of the most immediate concerns is the weakening of the concrete itself. Water can dissolve the soluble components of concrete, leading to a loss of mass and strength over time.
Moreover, water infiltration can lead to the corrosion of the steel reinforcement bars (rebar) embedded within the concrete. Corroded rebar loses its tensile strength, making the concrete more susceptible to cracking and spalling. In extreme cases, the combination of weakened concrete and corroded rebar can lead to structural failure, posing significant safety risks to both vehicles and pedestrians.
Recognizing the Signs of Structural Compromise
Early detection of water leaks and their effects is crucial for maintaining the structural integrity of a below-grade parking garage. Managers and owners should be vigilant in looking for signs of compromise, which can manifest in various ways:
- Cracking: Hairline cracks may appear on the surface of the concrete. While some cracking is normal due to the concrete's natural curing process, excessive or widening cracks can indicate a serious issue.
- Spalling: This refers to the chipping or flaking off of the concrete surface. Spalling is often a sign that the concrete has been weakened, either due to water infiltration or freeze-thaw cycles.
- Efflorescence: A white, powdery substance may form on the surface of the concrete. This is a sign that water is moving through the concrete, dissolving its soluble components, and depositing them on the surface.
- Rust Stains: These indicate that the rebar within the concrete is corroding. Rust stains usually appear as orange or brown streaks on the concrete surface.
Taking Immediate and Long-Term Actions
Addressing water leaks and their structural implications requires both immediate and long-term strategies. Here are some actionable steps:
- Immediate Actions:
- Seal Leaks: Hire an expert to seal leaks with polyurethane grout. This material is effective in stopping water infiltration and can even be applied to damp surfaces.
- Install Drainage: If water ponding is a problem, consider installing additional drains to remove standing water.
- Long-Term Actions:
- Regular Inspections: Schedule regular structural assessments to identify any new or worsening signs of water damage.
- Maintenance Plan: Develop a comprehensive maintenance plan that includes routine cleaning of drains and regular re-application of waterproofing materials.
Protecting Your Investment and Public Safety
The structural integrity of a below-grade parking garage is not just a matter of maintaining a physical asset; it's also about ensuring the safety of the people who use the facility. By understanding the detrimental effects of water on concrete and taking proactive steps to address them, stakeholders can protect both their investment and public safety. Ignoring the issue or delaying action can result in costly repairs, decreased property value, and, most importantly, compromised safety conditions.
By taking a proactive approach to water leaks, responsible parties can extend the lifespan of their below-grade parking garages, reduce maintenance costs, and ensure a safe and functional environment for users. The key is to act early, monitor regularly, and employ effective solutions tailored to the unique challenges of subterranean structures.
Want more information on sealing leaks with polyurethane grout?

