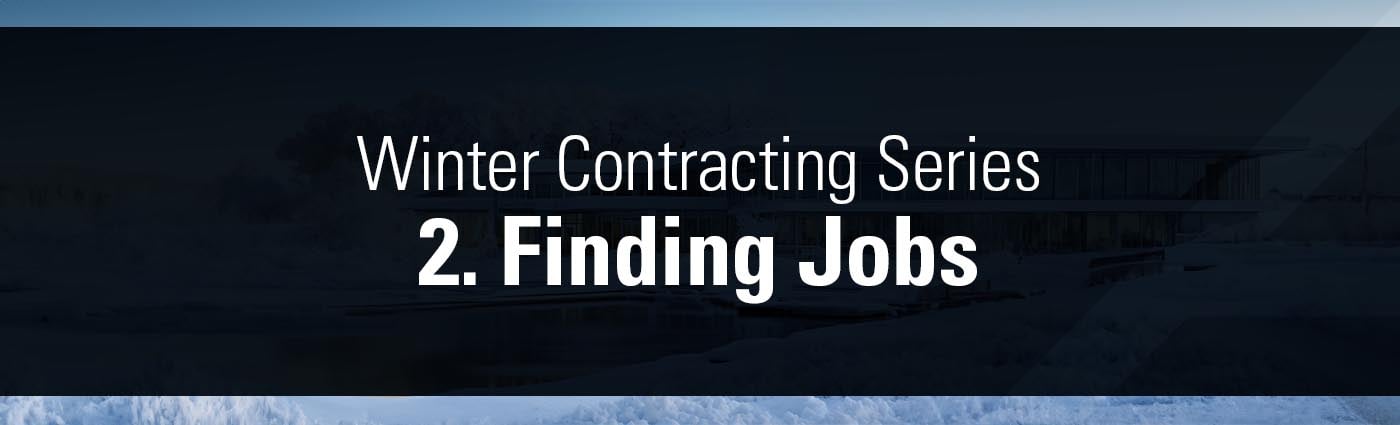
It's time to revisit the idea of remaining profitable during the winter months, but where does one begin?
Engaging with Engineers and Consultants
Networking with engineers is a cornerstone for securing a consistent flow of projects. Engineers are usually involved in any sizable geotechnical or waterproofing project. From industrial settings to property management companies and hydroelectric plants, an engineering firm is almost always the first port of call for problem-solving.
Alchatek offers presentations designed for engineers that cover a range of polyurethane applications like leak sealing, soil stabilization, and concrete lifting. These presentations often qualify for continuing education credits, offering engineers added value. We prefer to collaborate with local contractors for these presentations, creating a link between suppliers, contractors, and engineers.
With diligent follow-up, such activities typically yield smaller-scale projects, which, when successfully completed, pave the way for larger undertakings. Engineers are the go-to professionals for property owners facing issues. If you establish yourself as a reliable, punctual, and skilled contractor, you are more likely to secure jobs without having to go through the bidding process.
Networking Through Professional Associations
A wealth of professional associations exists across various fields and trades. Becoming a member provides an excellent platform for networking and discovering new opportunities.
Take, for instance, your local chapter of BOMA (Building Owners and Managers Association), which represents the expansive commercial real estate industry. BOMA members are mainly property owners, facility managers, and building engineers—a perfect audience for discussions on topics like elevator pits, parking structures, and tripping hazards.
IFMA (International Facility Management Association) is another noteworthy association. While BOMA represents the "landlords," IFMA represents the "tenants," who are often the first to report issues. Presenting to IFMA allows you to inform facility managers about problem-solving polyurethane technologies.
Don't overlook ASCE (American Society of Civil Engineers) either. It's not just for engineers; they offer a category called Organization Partners for non-engineers. Your presentation here can also be facilitated by Alchatek.
Reaching Out to Government Agencies
Sometimes old-school techniques like making phone calls and doing online research are invaluable. Connecting with local municipalities and Departments of Transportation (DOTs) can give you insights into upcoming projects. Attend bid meetings to network with general contractors and engineers.
Don't ignore mass transit authorities in cities with train or subway systems. These authorities regularly release projects for bidding and have engineering departments that could benefit from your solutions in leak sealing and geotechnical applications.
The cold months are an opportunity if you're a contractor seeking winter work. Not only will these strategies help you find winter projects, but they will also positively impact your business all year round. Reach out to the Alchatek support team for guidance.
For in-depth information on geotech polyurethane applications...

