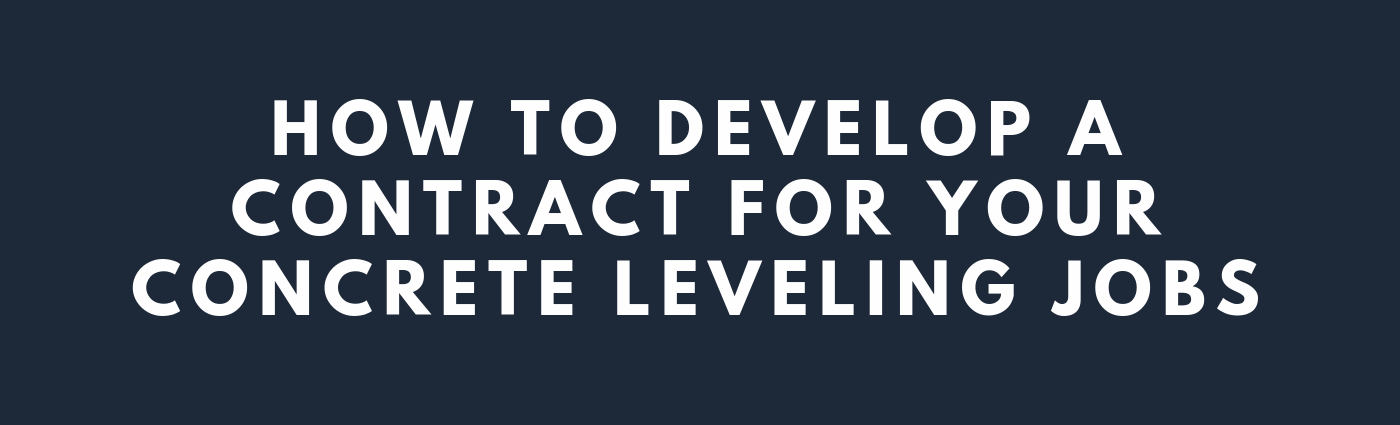
This blog post explains how to develop a contract for a typical lifting job. We’ll cover essential points such as Description of Process and Products, Scope of Work, Scheduling, Items Furnished by Others, Stipulations, Price, Warranty, Terms of Payment and Seeking Legal Counsel for Fine Tuning.
PLEASE NOTE: This article covers situations that you may want to consider when preparing your contract. It is not intended as legal advice, is not all inclusive, and has not been reviewed by any attorney. It should not be relied upon as such. Laws vary from state to state. You should seek the advice of legal counsel licensed to practice law in your state before finalizing your contract documents.
Brief Description of Process and Products
It’s important to start by outlining the process and products you’ll be using. Some of our current customers use blurbs like this…
The slab lifting process consists of the injection of expansive high density polyurethane foam underneath the concrete. This foam is manufactured by Alchemy-Spetec of Tucker, Georgia. This high density foam has a quick cure time of 15 minutes to 90% weight load capacity, does not shrink, is hydrophobic, creates a moisture barrier, and is lightweight.
Scope of Work
Next you’ll want to be very specific about the scope of work for the project. Use this section to explain to the customer exactly which areas will be lifted and exactly how you estimated the amount of material you’ll need. (For a refresher on estimating material, see our blog post Estimating Material for Slab Lifting Jobs.)
Scheduling
It’s important to spell out the order in which certain events will take place and the time parameters in which you’ll be able to do the work. For example, you may cover points like calling the appropriate agency to locate underground utilities on site before the job starts, coordinating with the engineer (if there is one) during the job, and outlining the days and hours in which you typically work. You can also let them know how long it will typically take you to begin the job after they give you the green light.
Items Furnished by Others
In this section you can briefly list any items that you expect the customer to furnish, such as access to and from the work area, electricity, water, etc.
Stipulations
It’s critical to inform your customer and also cover yourself regarding anything and everything that could go wrong on a slab lifting job. Unlocated plumbing pipes accidentally infiltrated with resin, cracks in foundations lacking steel reinforcement, cracks in slabs, etc. Be clear about what you will and will not be held liable for.
Warranty
Alchemy-Spetec warrants that our resin products will not deteriorate or shrink for a period of 10 years after the date of installation. You need to decide what type of warranty you will offer on your labor. Many of our contractors offer to replace any failed product for a period of 1 year at no cost to the owner, and then at a pro-rated scale after that. Be sure to exclude any damage done by acts of nature such as floods, earthquakes, hurricanes, etc.
Price
Spell out exactly how much you will charge for labor and how much you estimate materials will cost. You may want to break down the material cost into a per pound amount, so they have an idea how much extra they will be paying if you have to use more material than originally estimated.
Terms of Payment
Lay out the terms of your compensation, including an up-front deposit amount, how long the customer has to pay the balance. Many of our customers insist on the balance being paid upon job completion, to avoid any collection headaches.
Seek Legal Counsel for Fine Tuning
Again, it’s important to note that these are just general guidelines meant to assist you in constructing a contract of your own. Laws differ from state to state. Once you have a rough draft completed, we strongly urge you to seek the advice of legal counsel licensed to practice law in your state. An initial rough draft combined with feedback and fine tuning from an attorney will get you to a solid standard contract that you can re-use for many jobs to come.
Want a phone consultation to discuss your concrete leveling contract?
