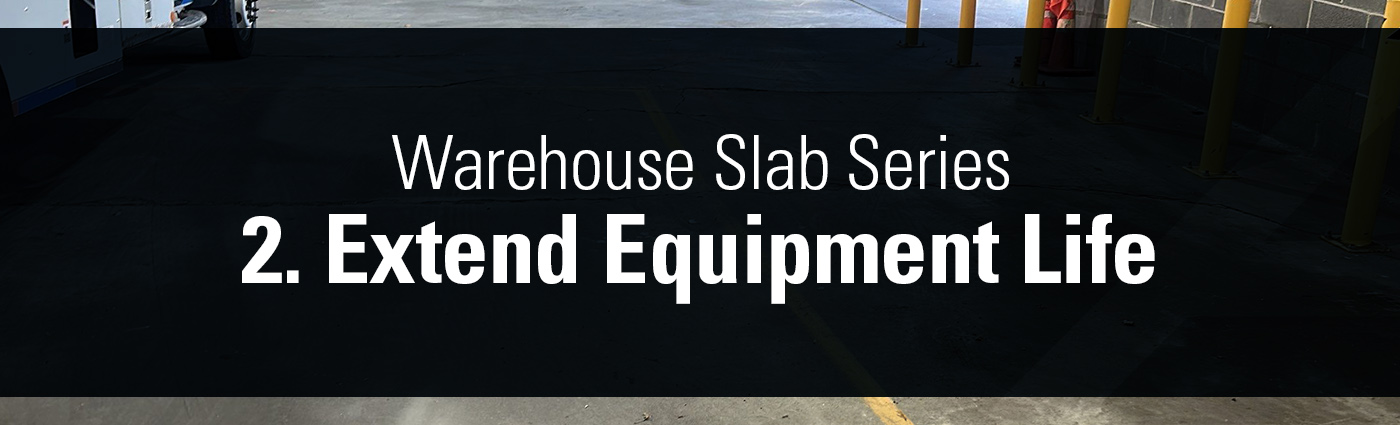
In a warehouse or distribution center, the condition of the floor can have a direct impact on the lifespan of material-handling equipment like forklifts, pallet jacks, and conveyors. Uneven or unstable floors can cause excessive wear and tear on these machines, leading to frequent breakdowns and increased maintenance costs. Over time, this can significantly reduce the lifespan of expensive equipment, necessitating premature replacements and adding to operational costs.
Polyurethane Slab Repair and Equipment Longevity
Hiring a contractor to stabilize and level sunken or unstable concrete slabs with polyurethane foam offers a unique advantage in extending the lifespan of warehouse equipment. A floor repaired with polyurethane foam provides a stable, even surface that reduces the stress and strain on machinery. Unlike other repair methods that may leave inconsistencies in the floor level, polyurethane foam creates a smooth, durable surface that allows for more efficient operation of material-handling equipment.
The quick-setting nature of polyurethane foam also means that equipment can be back in operation sooner, reducing the need for temporary solutions that might put additional strain on machinery. Furthermore, polyurethane's resistance to moisture and chemicals helps maintain the integrity of the floor, reducing the likelihood of future issues that could impact equipment operation.
Maintenance Savings Through Polyurethane
The cost benefits of using polyurethane foam for floor repairs extend beyond the immediate savings from reduced downtime. A stable, even floor contributes to less frequent equipment breakdowns, reducing the need for emergency repairs and maintenance. This can translate into significant long-term savings.
For example, the tires on a forklift will wear more evenly on a smooth surface, reducing the frequency of replacements. Similarly, conveyor systems will experience less friction and strain, leading to lower maintenance requirements. Over time, these savings can add up.
Actionable Advice for Warehouse and Distribution Center Managers
- Routine Equipment Checks: Alongside regular floor inspections, also incorporate routine checks of material-handling equipment. Look for signs of excessive wear or strain that could be attributed to floor conditions.
- Expert Evaluations: If floor-related wear and tear on equipment are suspected, consider bringing in experts for a thorough evaluation. They can provide insights into the extent of the problem and recommend appropriate solutions.
- Cost-Benefit Analysis: Before committing to any repair method, conduct a cost-benefit analysis that includes not just the immediate repair costs but also the long-term savings from extended equipment lifespan and reduced maintenance.
- Contractor Selection: Choose a contractor with specific experience in polyurethane foam applications for warehouse floors. Their expertise will ensure that the job is done correctly, maximizing the benefits for equipment longevity.
- Stakeholder Communication: Keep senior management and financial controllers in the loop about the long-term cost benefits of using polyurethane foam for floor repairs. Their support can be crucial for securing the necessary budget and resources.
By taking a proactive approach to floor maintenance and repair, and by understanding the benefits of polyurethane foam, warehouse managers can make informed decisions that contribute to operational efficiency and cost savings. The right repair method not only resolves immediate floor issues but also has a positive impact on the lifespan of expensive material-handling equipment. This dual benefit makes polyurethane foam an attractive option for managers looking to optimize both floor conditions and equipment longevity.
Want more information on lifting slabs with polyurethane grout?
