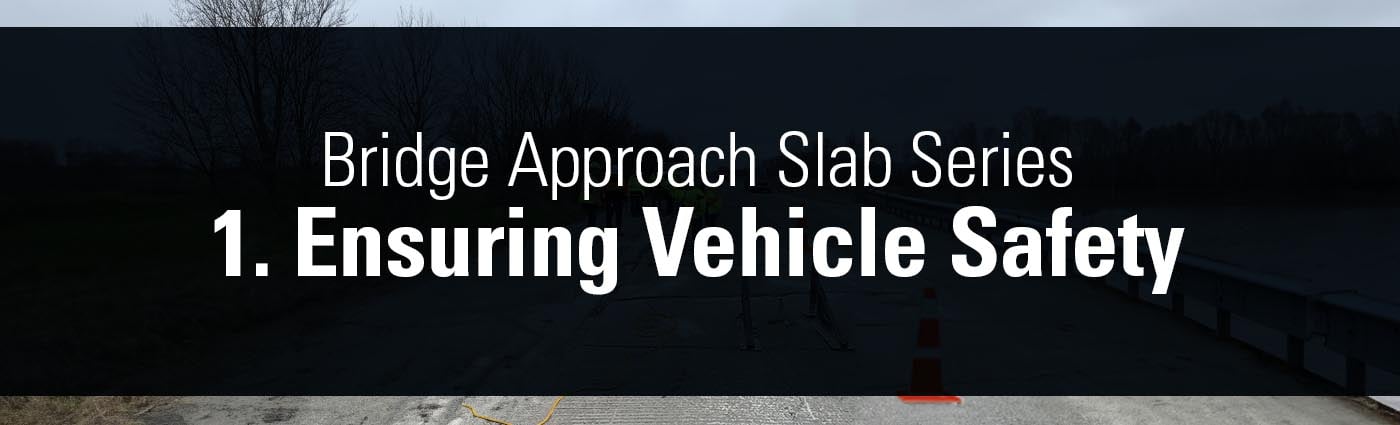
The role of bridge approach slabs in vehicle safety and infrastructure integrity is critical but often underestimated. When these slabs begin to sink, the consequences can be dire, ranging from vehicular damage to potential accidents. Such sinking typically originates from imbalances and instability in the underlying soil. It's not just an issue to be patched; it's about stabilizing the ground itself to ensure long-term durability and safety.
Understanding the "Bump" Problem
When bridge approach slabs become uneven or sink, they cause a height difference with the adjacent road or bridge deck. This manifests as bumps that are more than mere inconveniences; they are safety hazards. A minor elevation difference can create significant stress concentrations, leading to damaging impacts on vehicle suspensions and road infrastructure, particularly at high speeds.
Strategies to Alleviate Risks
Quick fixes like asphalt wedging may offer temporary relief but are not durable, leading to repeated maintenance cycles and increased costs. Polyurethane foam has emerged as a lasting solution, offering excellent compressive strength for soil stabilization beneath the slabs. Once cured, this foam provides strong and stable support, drastically reducing future sinking risks.
Quick Cure, Less Disruption
One advantage of polyurethane foam is its quick curing time. Traditional methods may necessitate extended lane closures, but polyurethane foam sets within minutes, allowing for quicker repairs. This minimizes traffic disruption, an often overlooked but significant concern for maintenance managers.
Polyurethane Foam's Versatility
Polyurethane foam is adaptable to various soil types and slab materials, coming in formulations customizable for specific project needs. Regardless of whether the soil is sandy, clayey, or loamy, the foam can be modified to provide optimal adhesion and compressive strength, mitigating the risks of slab sinking due to soil instability. Additionally, the foam has excellent water resistance. Hydrophobic formulations repel water, preserving the soil integrity underneath the slab—a vital feature in regions with high precipitation or prone to flooding.
Engineering Principles for Durability
The application of polyurethane foam is grounded in sound engineering. When injected, the foam expands, stabilizing the soil, leveling the concrete, and distributing the slab's load more evenly. This reduces point loads and stress concentrations, extending the slab's longevity and the overall durability of the bridge-to-road transition. The foam's adhesive qualities create a monolithic structure between the slab and soil, rendering it resistant to future shifts. This quality is invaluable in seismic-prone areas where ground movements can compromise infrastructure.
Cost-Efficiency
While polyurethane foam has slightly higher upfront costs compared to traditional methods like mudjacking, its durability makes it cost-effective in the long run. Reduced maintenance cycles and the speed of application minimize both direct and indirect costs, making polyurethane foam an economically sound choice.
Safety Protocols in Application
Safety is paramount during the foam's application. Engineers and crews must wear appropriate Personal Protective Equipment, including gloves and eye protection. Specialized equipment must be used for the foam injection, and staff should be well-trained to prevent over-injection, which could lead to additional stresses and imbalance.
Ensuring Vehicle Safety
Addressing the challenges of sinking or unstable bridge approach slabs significantly enhances vehicle safety. Polyurethane foam emerges as a multi-faceted solution that not only mitigates immediate risks but offers long-term durability. Its quick curing time, adaptability, and engineering advantages make it an essential tool for infrastructure teams committed to the highest safety standards.
Want more information on geotech polyurethane grout applications?

