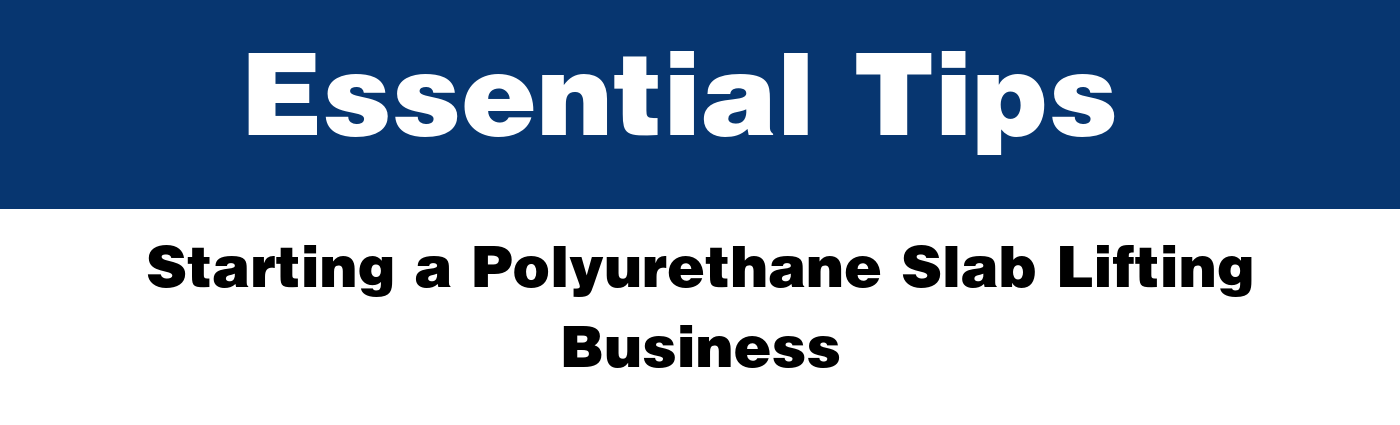
Pursuing the dream of starting your own polyurethane slab lifting business is a big leap. But it's not nearly so intimidating when you're armed with the right information. In this post I'll cover available slab lifting markets, marketing strategies for your lifting business, and estimating materials for a job.
.png?width=300&name=Copy%20of%20Essential%20Tips%20(1).png)
Polyurethane Slab Lifting Markets
Residential Slab Jacking
The residential market offers tremendous opportunities for the slab lifting contractor. Obviously there are driveways, foundations, patios, pools, and porches. Don’t think residential only includes houses. There are countless opportunities in the apartment and condo sectors as well.
Commercial-Industrial Slab Jacking
Because scenarios for slab lifting are infinite in the non-residential category, we list commercial and industrial together. Concrete parking lots, showroom floors, industrial park walkways and an endless supply of huge warehouse floors are just the tip of the iceberg in this potentially lucrative market.
Slab Jacking for the Transportation Sector
Last but not least, there's the transportation sector. The world is covered with miles and miles of concrete roads, highways, bridge approach slabs, and railroad support slabs. A large percentage of them have settled in one spot or another (and the rest are vulnerable to future settling).
Read more in the post Identifying Common Markets for Slab Jacking with Polyurethane.
There will NEVER be enough slab lifting contractors out there to address ALL of these current and future slab lifting needs. Your fortune awaits...(IF you know what you’re doing).
Marketing Your Slab Lifting Business
Maintaining A Well Designed, Search Engine Optimized Website
Professional design, photography and content will help you stay competitive and either depict you as a confident, articulate leader in your field or just the opposite (if it's not well designed). It is also imperative to make sure that your website is Search Engine Optimized. Designing a search friendly site for your industry niche and market location will make a world of difference in the amount of leads you capture via your online presence.
Attracting Leads with a Blog
Posting blog articles regularly allows you to cast a wide net with lots of SEO friendly post pages. It's also a great way to share your knowledge and build trust in the market as an industry expert. If you offer more value (such as an info-packed brochure) in exchange for contact info, you can increase your leads dramatically. Blogs are a gift that keeps on giving, because the posts stay up and attract new leads forever. Read all about this extremely effective marketing technique in our blog post How to Promote Your Contracting Business with a Blog.
Targeted Local Advertisements
Setting up a Google Ads account to target your market and placing ads in local publications are effective ways of getting the word out in your local market. If you’re aware of a specific problem occurring in your area, such as sinkholes, you can even highlight that issue in your advertising. Read more marketing tips in the post Marketing Your Slab Lifting Business.
Advertising on Contractor Referral Sites
Because you’re putting yourself in front of customers who are actively seeking your services, you can increase your marketing ROI compared to other methods such as cold calling, print advertising, etc. In addition, referred customers are typically less price sensitive than cold call prospects. Referral sites are also a great way to build your reputation by accumulating positive reviews from customers. Read more about this approach in our blog post How to Market Your Contracting Business with Referral Sites.
Exhibiting at Home Shows
Home shows are a great place to meet potential customers and even affiliate partners. Contractors tell us over and over again that home shows are a GREAT source for leads. Take a look at our blog post on marketing at home shows.
Presenting at Professional Associations
Giving presentations at local chapters of professional associations is a great way to network, meet potential customers and lead sources. Look into organizations serving property maintenance professionals, building managers, property owners, real estate professionals, etc. Establish yourself as a local expert and people will come to you when they have slab settlement problems.
Estimating Materials for Jobs
Material Calculation
Through a combination of easy calculations, product information, and some site considerations, you should be able to estimate your slab lifting materials without too much trouble. Fortunately, Alchemy-Spetec has a simple estimating app that allows you to calculate the lifting material you'll need in a few easy steps. Read the blog post on our estimating app for more info.
Specific Considerations
Beyond the geometry required to estimate lifting the slab, you must take into account some job specific considerations. This is where it becomes critical to qualify the volume of material included in your proposal. And just as important, this is where you need to make sure you have included enough so you get the job done right and don’t have to go back to the customer asking for more money. Sometimes that’s unavoidable if you encounter surprises; but by keeping a few considerations in mind this can often be avoided. For help on specific considerations, contact your tech support rep at 404-618-0438 today.
Include Contingency Material
Typically for a lifting job without other considerations besides the lifting volume, we recommend adding an additional 10- 15% onto your material estimate to cover yourself. Just make sure you do a thorough evaluation of the conditions and possibilities so you don’t underestimate the job and have to go back to the property owner with your hand out. Read more in the post
Estimating Materials for Slab Jacking.
Want more information on slab lifting?
