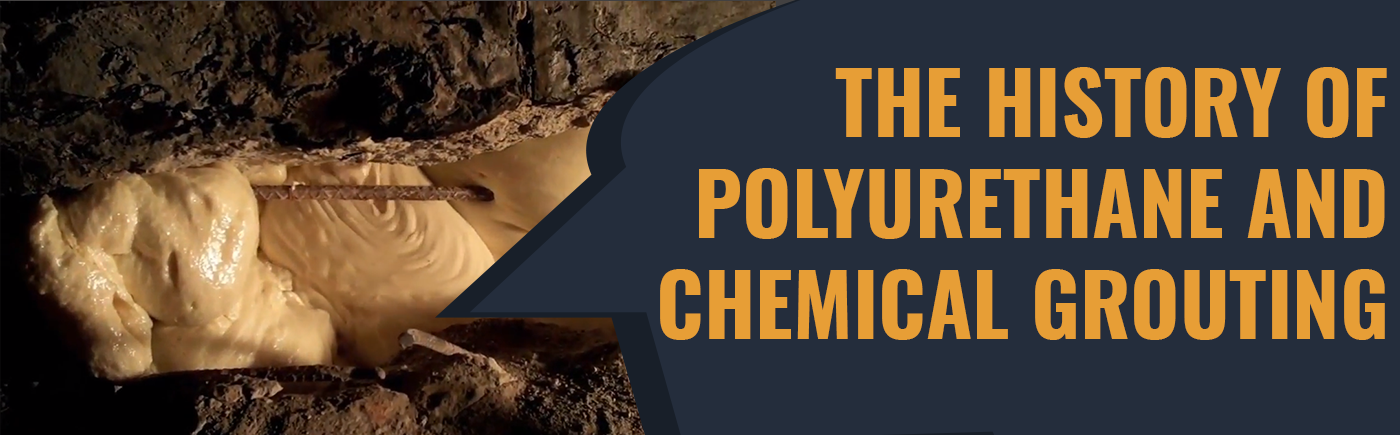
After three decades in this industry, I still find myself in awe of what polyurethane foam can do. From sealing massive dam leaks to stabilizing airport runway slabs to lifting entire buildings – the feats contractors achieve with this stuff is astonishing. Yet some people who are new to this technology have a hard time understanding how a mere “foam” can be ideal for these most demanding of applications. Or maybe they wonder how safe it is.
The irony is, whether you think you are “new” to this technology or not – you’ve been surrounded by polyurethane all your life. Sometimes an understanding of the past can provide more confidence for moving forward into the future. So if you can’t quite grasp how “foam” has been developed to the point that it can lift a building – or you wonder how safe it is – pay close attention to this story.
Dr. Otto Bayer first made polyurethane foam in Leverkusen, Germany in 1937. Polyurethane was initially used as a cheap replacement for rubber. Widespread use began in World War II, when many other materials became scarce. Polyurethane use quickly spread as a key component in many products, from specialized paper to protective military garments to gloss finishes and protective coatings.
In the 1950s, many companies such as DuPont, BASF, Dow, and Union Carbide started producing polyurethane for an even wider variety of applications including adhesives, insulation and foam upholstery cushions. In the 1960s the Bayer company (no relation to Dr. Otto Bayer) exhibited an all-plastic car, parts of which were made with polyurethane.
In the early 1970s, the introduction of polyurethane skateboard wheels as a replacement for the old metal ones completely revolutionized the sport, as the new wheels allowed for high impact activities such as jumping off of ramps. In the 1980s, the first mass produced plastic-body automobile – the Pontiac Fiero – was made with the use of polyurethane technology.
Today polyurethanes can be found in an infinite amount of products including furniture, clothing, shoes, beds, moldings, etc.
In the 1960s, 3M Company in the U.S. and Takanaka in Japan both introduced polyurethane grouts. 3M’s product was called Elastromeric Sewer Grouting Compound. As the name indicates, it was intended for use in underground utilities. Takanaka’s product was called Takanaka Aqua-Reactive Chemical Soil Stabilizer (TACSS). As the name indicates, it was intended for use in soil stabilization projects. In the early 1980s, DeNeef obtained the rights to TACSS and began distributing polyurethane grout worldwide. By the mid 1980s, there were almost a dozen manufacturers of polyurethane grouts. I got my start pumping 3M 5600 to seal cracks in the Atlanta subway system back in 1985. I was amazed at what it could do back then, and I am still amazed at what our products do today. 3M exited the business many years ago.
In the last few decades, polyurethane grouting has become a widely accepted method for sealing leaks, stabilizing soil and lifting slabs. Many innovations have been made, including closed cell hydrophobic polyurethanes and the use of two-component foams in geotechnical engineering. Polyurethane’s advantages over the old school approach of cement grout repair is covered thoroughly in our blog post Polyurethane vs. Cement for Slab Jacking.
Want more in-depth info on polyurethane and chemical grouting?

