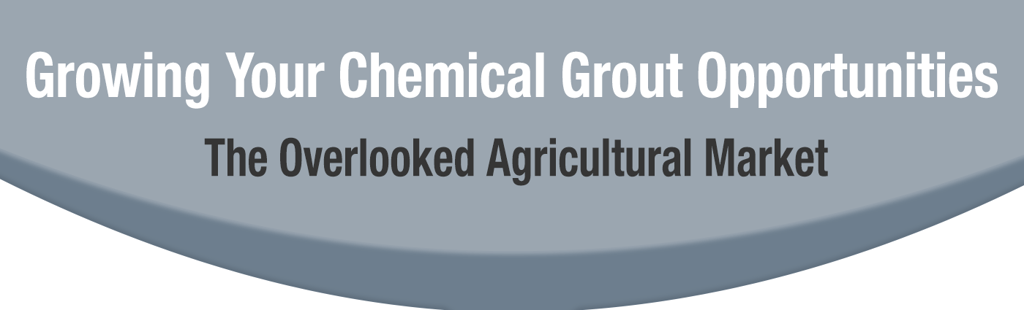
I’m a big proponent of using chemical grout to fix all sorts if issues, be they geotechnical or waterproofing related. Most contractors and distributors that offer chemical grouts fall into one or more of the following categories: Residential Slab Lifting and Foundation, DOT Infrastructure and Roads, and Municipal Storm and Wastewater. Certainly, there are some others, but these are the main ones we see.
As the popularity of slab lifting with polyurethane continues to heat up, there is more and more competition for residential business. With the ability to electronically access bid data across the USA, there are few secrets; all the big players know about the DOT work and water treatment plant expansions, etc.
Why work so hard fighting over the same pie everyone else knows about? How about baking your own pie?
A healthy population depends on access to clean water and a healthy supply of food. North America is a world leader in producing both. The US and Canadian agricultural industry though, remains untapped by specialty concrete repair contractors and their suppliers. Rather than tell you where to look for opportunities in "Big Ag", let me share an example in which I found myself advising a customer who was installing polyurethane. This example will be enough to get you thinking...
Three stories below ground level I saw a stream of water shoot all the way across a grain bin. I was in the great plains of Canada in the lower levels of a grain terminal. With a capacity for receiving 800 tons of grain per hour; and the responsibility of drying it and storing it, the owners of this terminal could ill afford water intrusion issues. Twin rows of belly dumping grain haulers pull into the facility on a regular basis and drop everything from wheat, barley, peas, lentils, etc.
The noise was deafening as the hard seeds cascaded down through the facility into hoppers below. The problem in this hopper was slow water intrusion seeping into the bin. The effect was twofold as the ceramic wear plates that protect the steel were delaminating, and the incoming grain was getting wet. This made it harder for the augers and grain elevators to work properly, created a health risk, and created a lot of manual shoveling in a confined space environment.
The stream of water came from our contractor's first drill hole, an indicator of how much hydrostatic pressure surrounded the hopper. We had to overpower this pressure with some pressure of our own. Twin streamed warm water and AP Fill 700 (maxed out with 10% Cat 107) reacted instantly and were already making foam as they entered the cold 48 degree water surrounding the hopper. A thorough application of between 50 – 75 gallons encapsulated the bin we were in and pushed away the water. The ceramic tiles dried up and the owners were ecstatic; they did not even ask what it would cost because they had no other solution. To replace or reline those bins would have been next to impossible or would've required massive downtime and disassembly of everything above the bins. We, on the other hand, solved the issue in one day. Appropriately, a “grain themed” celebration was held after the job was over later that day with cold beer and Irish Whiskey!
The point of telling this story is to make you aware that there is a huge untapped market out there, full of people who need the solutions your business offers. Whether it is stabilizing soil under slabs and structures or stopping water intrusion. Just about every state and province has major agricultural business going on, including crops and livestock. I won’t speak for everyone, but I would wager that most contractors are not calling on those types of facilities and businesses. Instead of waiting for the phone to ring about another driveway lift; make someone else’s phone ring with some good news about chemical grout. Do this consistently and I don’t think you’ll be disappointed.
Need more information on Alchemy-Spetec products?

