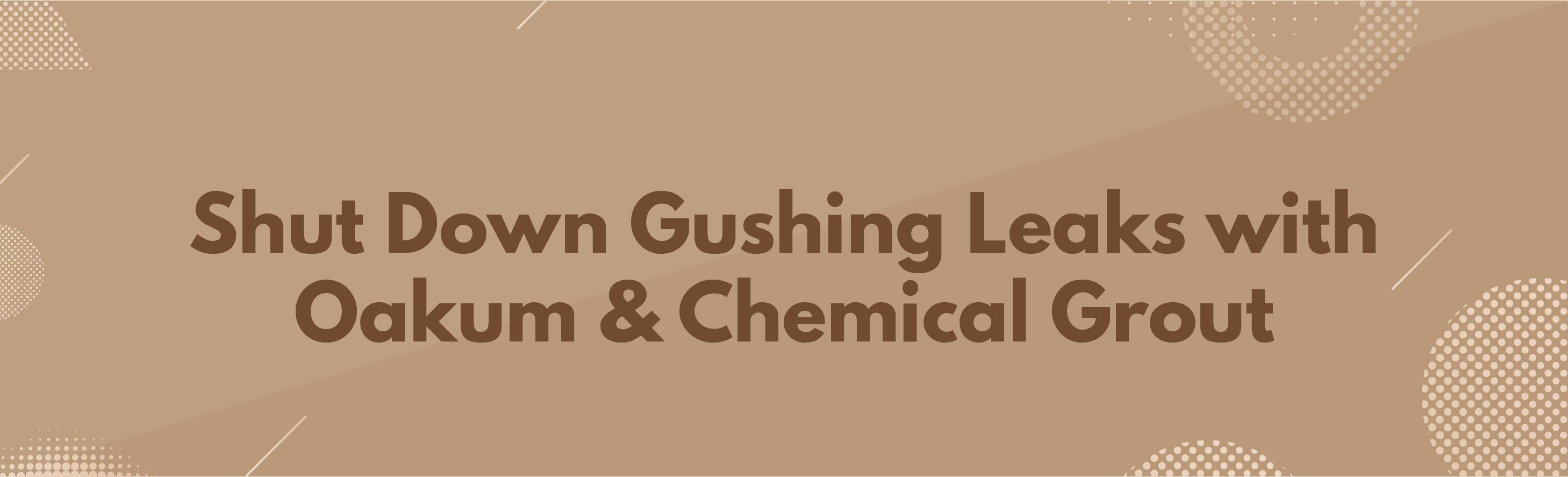
Polyurethane chemical grout injection can be a bit of a Pandora’s box at times. So, what can be done to help combat some of these uncertainties? Well, how about the easiest and most cost-effective solution first. Oakum! Not only is it amazing what you can accomplish with it, but it is vital to have on every job. YES, I SAID EVERY JOB.
There are only two things that have to happen for successful water mitigation. One, get the grout to the right location. Two, keep it there long enough to react. With tight cracks, it can be difficult to get the grout to travel in the crack, but once you get it there it is good to go. With wide cracks or high flow leaks, getting to the right place is easy, but keeping it there long enough to set up can be challenging.
You can use oakum to control grout and keep it where you want it in the crack or joint. Remember we are doing the injection work to stop the flow of water, so let’s make the least amount of holes possible in the concrete. But what does that have to do with oakum? Cracks are irregular, and often have sections that are wider in some sections. When this wider area is at the surface it can allow an easy escape path for a grout under pressure. That means you are wasting grout and not getting it where it needs to be, deep in the crack. Sure, if you have raw resin coming out of the crack you can just wait for it to cure. Once cured you cannot reinject that packer, so it is best to surface seal that crack and stop or slow down the loss of grout. This allows you to continue effective pumping into the crack or joint.
If the crack or joint is wide, grout impregnated oakum can be packed in place. While messy, this is the equivalent of finger painting with chemical grouts and is an easy process.
If you're thinking "I have rags, I don’t need oakum", think again. Oakum is stronger, can be pulled apart into just a few fibers if needed, and can be stuffed into very tiny defects where rags cannot fit.
Want more information on leak seal products?
