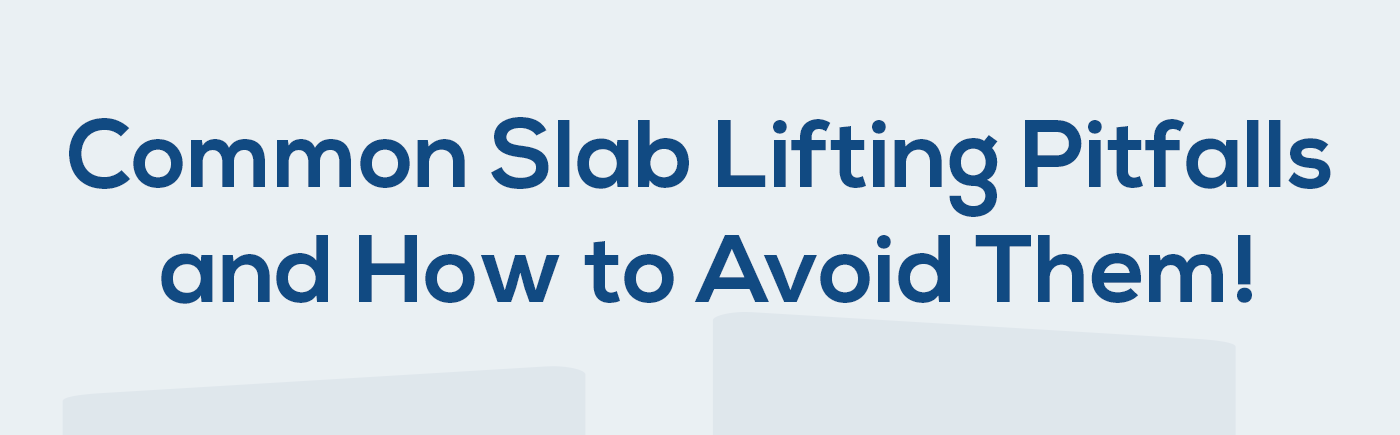
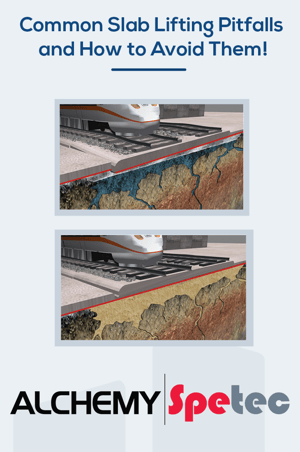
This last year has been crazy busy; we have been on so many slab lifting projects with our contractors. From residential to commercial/industrial, slab lifting with polyurethane is proving to be a huge success. However, there are some patterns that have emerged in terms of the challenges that contractors face. Probably more than 99% of slab lifting jobs go just fine, but these tips should help you maximize your results.
Something’s Gotta Give - Bound Slabs
The AP Lift series of polyurethanes are very powerful; capable of lifting slabs several feet thick. So if you suspect you have a slab that might bind or hang up, you need to take precautions. Otherwise you risk breaking it. In this business you’re going to deal with control joints, expansion joints, and cracks (both hairline and major). You have to do your best to clean them out. A proactive saw-cut on a joint might make your life easier. Routing out a joint or a crack with a diamond sawzall blade, a thin trowel, or some compressed air is going to pay dividends. Lubricate joints, cracks, and edges with AP Flush 125 for rapid results.
Heavy Structures with a Small Footprint
These types of lifts are the toughest. A typically sized two foot thick slab with equipment on it will often come up easier than a set of front steps, a chimney, or a footing. Polyurethane foam likes to have a little bit of room to spread out and lift; when there is concentrated weight on a small base, the poly will try and squeeze out the sides. If the soils are soft or water saturated, it is even more challenging.
Try making the foam work for you. Use short, controlled shots of material that don’t travel very far. Inject a few perimeter shots to create a damming effect that will retain additional foam injected inside of the perimeter. Finally, don’t be afraid to use some mechanical assistance. There have been some unique lifts of this type done with the help of various jacks, levers, and beam systems.
The Wrong Part of the Slab is Lifting
I was on an interesting sidewalk slab lift project awhile back. We had finished several jobs over two days and were feeling pretty good about things; so I wasn’t paying close attention. My contractor, however, was paying very close attention to the joint where he was trying to get lift. So much focus that he did not notice the slab was actually lifting behind him and not where he wanted or anticipated it to.
So how do you avoid this? First of all keep your head on a swivel. ALWAYS be paying attention to what is going on around you – looking for movement, escaping foam, cracks developing.
Secondly, be patient. Use short controlled shots of foam, let that material set up and gain some strength. Then drill through it and inject more material below. This keeps it concentrated in one area instead of allowing it to push under areas you don’t want to lift.
Third – monitor the slab at various points with dial indicators, zip levels, string lines, or laser transits so you know what is going on at multiple points. And last of all, perhaps that joint that won’t move is bound and needs to be saw cut.
Cracking the Slab
If you have worded your contract correctly, you should have some language covering you in case cracks appear while the slab is being lifted. Concrete slabs crack as they settle so it is logical to assume that they may crack when being raised. To keep cracking to a minimum, here are some tips:
- Short controlled shots of material – no need to be in a hurry – constantly monitor the slab for movement.
- Use common sense – a long slab will need support as it is being lifted. I usually start at the lowest point and start my injections there. I will spread out and hit other points and bring the slab up gradually. As it is lifting it will create voids that need to be filled with supporting foam.
- Know when to stop – sometimes it is that last shot of material that cracks the slab. You are trying to get that last 1/10th of an inch lift to make it perfect and the slab doesn’t want to move; then a crack appears. If a slab stops moving it is probably binding, and this can sometimes occur right when it is a hair from being back in place.
- Last of all, don’t panic if you crack the slab. If you act or look like you just did something terribly wrong, the property owner will pick up on that and then you may have an issue. The slab you just lifted is now supported and stabilized from below; the crack is not a sign of something wrong. Usually the cracks that occur are of the hairline variety and will often close right back up as you complete the lift. So be cool!
Property Damage
Damaging someone’s property is a sure fire way to turn a profitable day into a loss. The main type of property damage I have seen is from getting polyurethane on things that you’re not supposed to. Keep these tips in mind:
- Don’t pull off an injection point too soon. Let the material get its initial set before removing the port or the gun. This is the most common way to get foam on yourself and others.
- Don’t get too far ahead drilling holes. So many contractor crews I work with have one guy who wants drill all the holes before the other guy even starts injecting. Unless this is a giant warehouse job; don’t be in such a hurry. Too many times I have seen foam shoot out of an uncovered drill hole and get all over something. If you insist on it, then place dowels or plugged ports into those holes to prevent a blowout.
- Cover stuff with plastic – take the time to do this. And even better, create a simple shield to go around the injection gun. A 30 gallon plastic garbage can with a doghouse opening cut into it makes a very effective containment shield.
- Do your gun and hose maintenance in the rig, not on someone’s driveway or pool deck. B side drips typically clean up with water; A side drips however, clean up with time or money.
Over-Lifting
So you have gone and over-lifted a slab. Welcome to the slab lifting hall of shame – ha ha. This is one of the questions that I get asked a lot: “What happens if I over-lift a slab?”
In all my years of consulting, I’ve heard of this happening only a handful of times - and I’ve only witnessed it once. Lifting with polyurethane is very precise. Slab lifting doesn’t typically get out of control. With short controlled shots of material (do you sense a theme here?) you can anticipate how much a slab will continue moving after you stop injecting.
Monitor the slab in multiple places and keep your head on a swivel, as I recommended earlier. If you’re lifting near a doorway, constantly check the swing of the door to make sure it isn’t starting to stick. Take your time, think through what you’re doing, and you are unlikely to ever over-lift a slab.
Want in-depth info on slab lifting procedures and products?
