Perhaps the most misunderstood functionality of mechanical packer design is the ball-valve placement. The ball-valve placement is important because this is the functional element that keeps chemical grout in the substrate as it reacts and creates the density required to adequately seal the substrate. It is an applicator error to remove the packers prior to full product cure. Top-mounted zerk-valve packers allow for port-to-port travel observation. Port-to-port travel is injecting one packer until chemical grout is observed exiting the next packer which does not have an anti-return zerk-valve installed. Once the material is observed coming out of the next packer, the zerk-valve can be installed, and the process repeated (see FIGURE 7). This is only possible with top-mounted ball-valve placement. Another benefit of the top-mount packer is the ability to replace the standard zerk-valve with a button-top-valve (see FIGURE 8). Button top valves, as mentioned above, minimize leakage with a more secure connection to the packer that doesn’t allow the coupler/packer connection to flex (see FIGURE 9).
Bottom-mount ball-valves (as seen below FIGURE 10) are less common in the industry. The main benefit of bottom-mount ball-valves is the immediate removal of the top shaft following injection, and subsequent patching of the drill hole with the ball-valve still in the substrate. Bottom-mount ball-valve packers commonly have a bit more leakage and excess chemical grout as the shaft, above the ball-valve, is full of unreacted and unconfined chemical grout.
Alchemy-Spetec supplies a complete offering covering all of the functionalities detailed in this brochure. Below is a table detailing bottom-mount options and top-mount options. Note: All top-mount options can be converted to button-top style with by adding the equal quantity of Button-Top Fittings, ACP-2203.
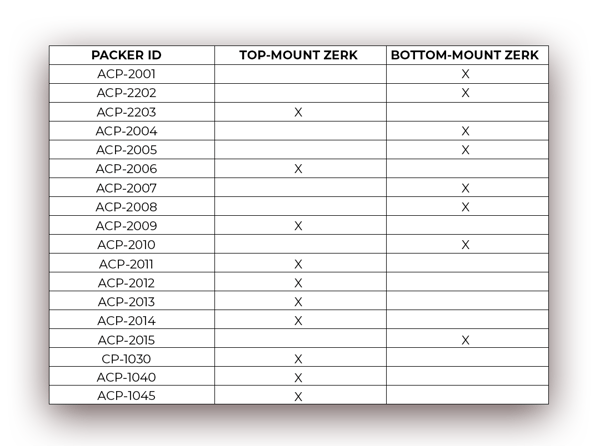
Want more information on mechanical packers?